Iterate to Innovate
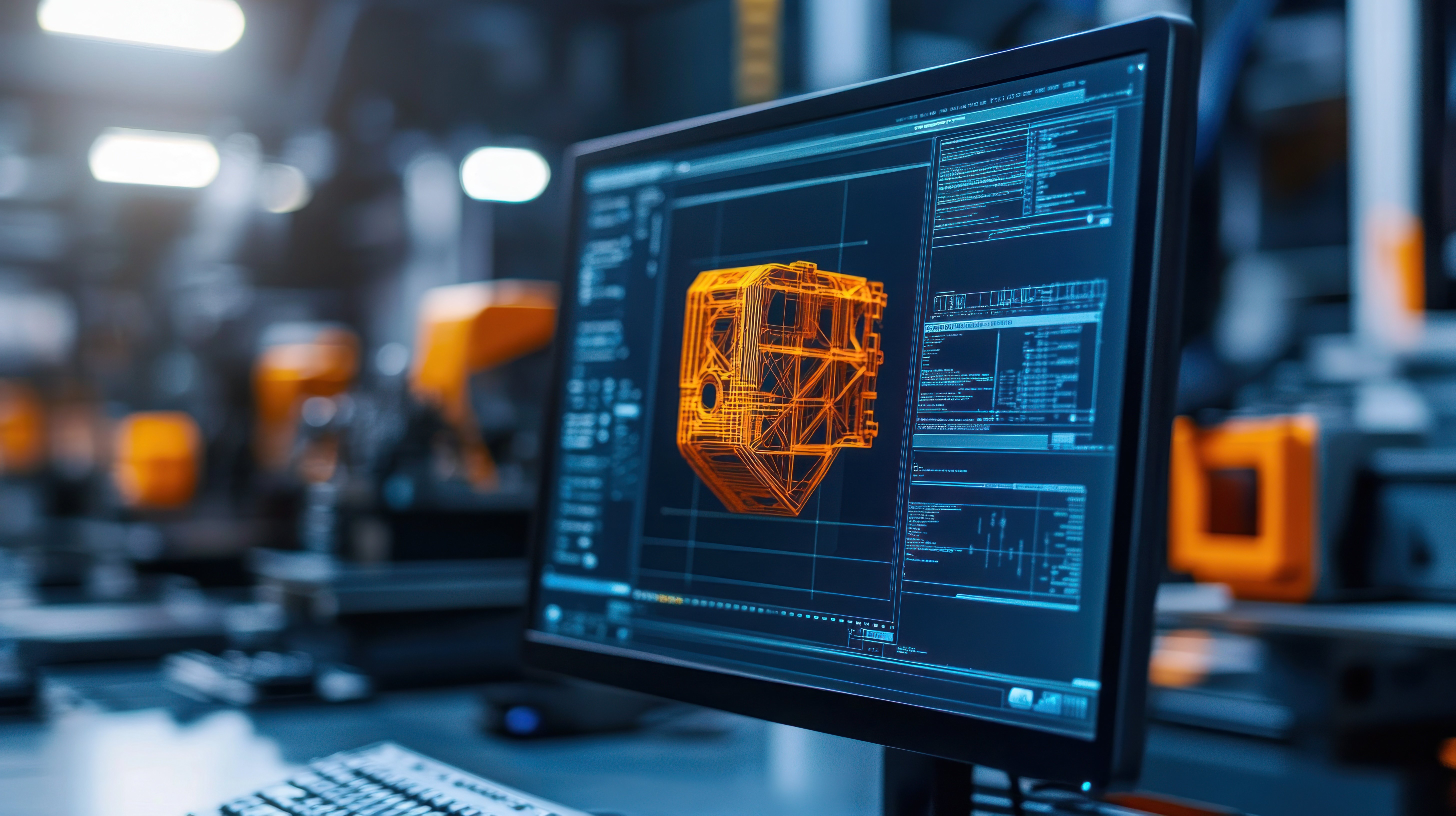
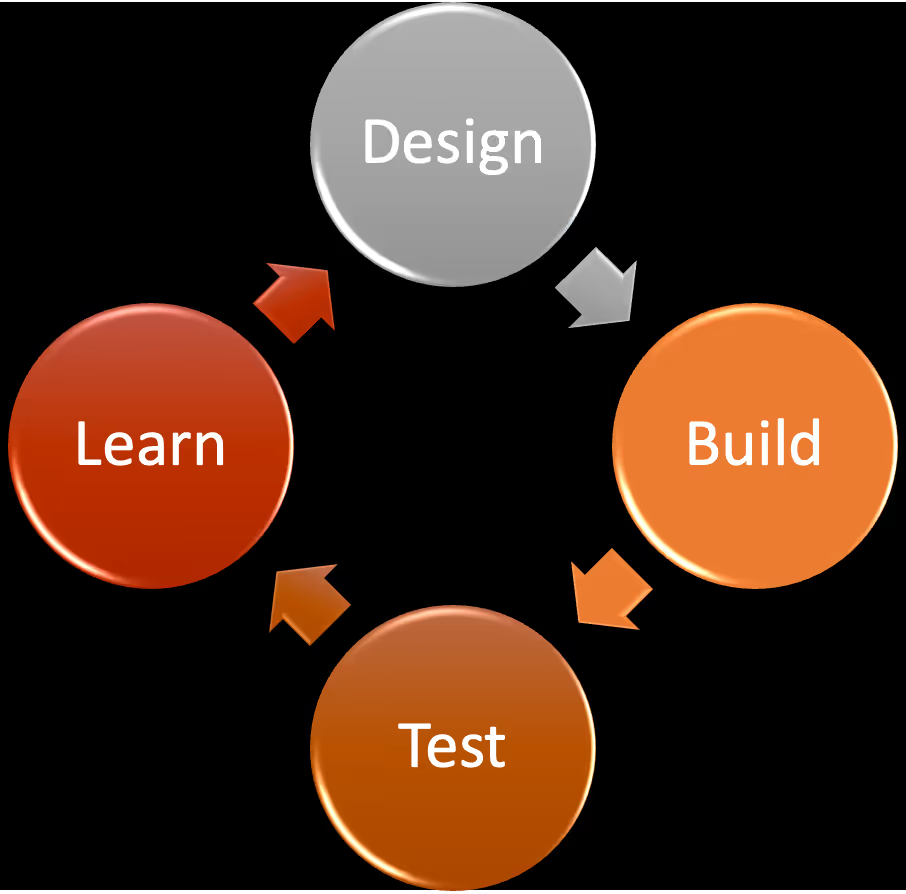
Baby steps.
I recently interviewed Paul Marotta from MicroNuclear LLC for the YPE Podcast. We’re developing the podcast to generate a series of episodes on SMRs and microreactors as a way to alert the public and broader energy industry of how many different designs and technologies are currently being developed with the end goal of being commercially deployed everywhere in the world. While the entire episode will be available publicly soon, a post is warranted to summarize the highlights in the interim.
Key Takeaways
- Driving Principle: Nuclear power is the energy best solution for humanity because of its energy density. It possesses the most bang for your buck, and the underlying physics will make it the most profitable long term. Because it’s best from a first principles perspective, we should build more of it – everywhere.
- Strategy: Chase the best technology designs and opportunities available which have the greatest chance of success. Don’t spend time attempting to recreate the wheel from scratch, but rather leverage what’s already been done before. Start from a realistic beginning with a sampled technology, and then do whatever it takes to innovate on it and advance it. Specifically, go build something, test it, redesign it, and test it again and again and again. In other words, iterate to innovate.
the undercurrent of any new technology:
“How is this going to be profitable?“
Much has been written on the driving principle that nuclear is the future. As a practical and pragmatic guy, I’d like to focus on the how of where we’re going rather than the why. The why is radically clear to me. People need energy everywhere – so let’s help them harness it. But how?
Technology is an incredible tool humans have leveraged and utilized throughout our evolution; however, it doesn’t build itself. There are no man-made tools which have been created that weren’t inspired or derived from previously made tools. In a word, we innovate to improve.
An interpretation of innovation runs rampant through the collective consciousness. Many believe to innovate is to have a huge and fundamental step change which has massive and unbelievable impacts on the way people do business, transport themselves throughout the world, or even fight. This couldn’t be further from the truth.
Real, rapid, and ingenious innovation occurs by taking baby steps – lots of baby steps. The small, incremental changes taken when trying new things inspires people to see a different way of accomplishing a task. There are often many roads to a successful outcome, but there are more dead-ends. Many times the dead-end routes have to be traversed in order to understand they lead to nowhere.
Let’s use diesel engines as a classic example. Just last week, I attended a training course for Project Managers and Engineers put on by the world renowned engine designer and manufacture, Caterpillar, in the beautiful and sprawling metropolis of Midland, Texas. The objective of the training was to familiarize attendees with the fuel burning process and critical failure points in Caterpillar’s new Dynamic Gas Blending (DGB) internal combustion engines. The engines are designed to burn both natural gas (mostly methane with small amounts of ethane and propane) and diesel fuel to allow consumers to exploit a price arbitrage between liquid and gaseous fuels. Sounds simple, right? Just light natural gas on fire instead of diesel!
It’s not simple.
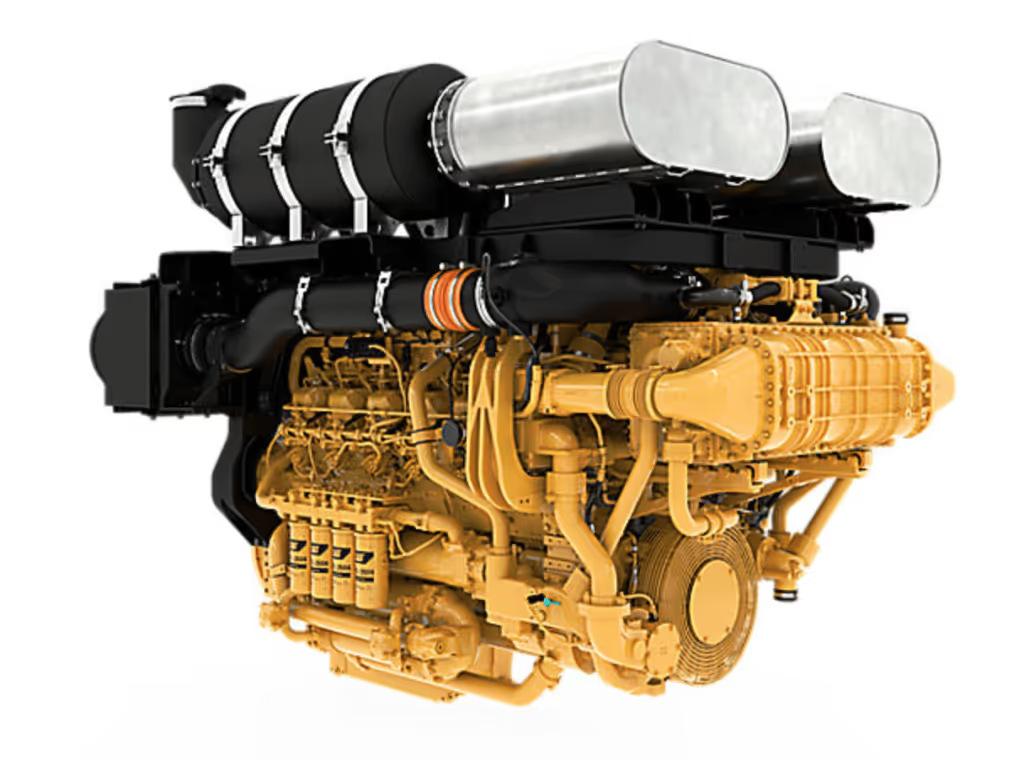
To someone who’s mechanically inclined, digesting the process and understanding how the entire mechanical assembly functions requires about 15 to 30 minutes to explain. However, you’re going to need more time to explain to customers of the million-dollar-machines why they’re only getting 10% natural gas substitution instead of the promised 70% substitution (i.e. 70% of the fuel blend is natural gas).
Each engine has at least 20 primary sub-assemblies, and each sub-assembly has between 4 and 50 components. Additionally, the entire system contains two on-board computer and monitoring systems. The entire system is a tremendous feat of engineering which deserves accolades and praise for the ingenuity and effort put into it. But consider this: every single one of those components had to be designed by an engineer who made design choices based on previous experience.
I’ll highlight two “innovations” covered during the course.
- Melting Computer
- Overview: one of the electronic control systems was originally placed on top of the engine near the turbo. Why place it there? It was convenient and close to the systems it was monitoring; however, a tragic oversight came into play with that placement choice.
- Problem: When the engine was in full operation, the objective of the turbo was to super-heat the air and fuel mixture to increase efficiency of the engine. The heat generated from this process wasn’t isolated and transferred quickly to everything around it – including the control system. How much heat? Think 1,000 degrees F. How hot does it need to be for your iPhone to start melting? That’s right – about 120 degrees F. See a problem here?
- Solution: Place the computer somewhere (almost literally anywhere) else on the engine. They decided to place it on the side. It was a simple redesign that could be implemented quickly to improve the performance. That’s innovation.
- Check Valve Replacement
- Overview: included in the flow path leading to the cylinders of the engines is a “check valve,” which is a common term for a valve designed to only allow flow in one direction. They’re common in literally all plumbing applications.
- Problem: If the inlet natural gas is not “dry and clean” aka is not pure methane, ethane, and propane but rather has small amounts of water and heavier lubricants in it, then it can contaminate and clog parts of the system – including this check valve. This was identified as a common failure point that would be difficult to “engineer out” of the entire system.
- Solution: While the root cause is poor quality gas and should be addressed upstream of the entire engine assembly, a workaround was identified for customers to use. The placement of the check valve was modified slightly, and it was re-designed to be replaced rapidly during operations. All a mechanical would have to do is unscrew four bolts, take the check valve out, pop a new one in, and the engine could function again. That’s innovation.
These two examples highlight how important experience is when improving engines. Internal combustion engines are over 100 (150?) years old. Scientists, engineers, and mechanics have been innovating and improving on them for literally over 100 years, and they still find ways to make them even better.
Now pivot the application of innovation to nuclear power. How is it possible to innovate rapidly, attempt something a thousand times, and discover the best possible solution when you’re only building one prototype? When you’ve only built one power plant? When did you, your team, your customers, or the end users of a technology have the chance to improve on the roadmap to construction, eliminate unneeded steps, establish better timelines, leverage previous experience, and correct thousands of previously made mistakes?
This is the tragic story of what’s occurred at the Vogtle facility, and it’s the true promise that SMRs and microreactors bring to the world.
The merits to SMRs and microreactors are many, but the biggest benefit to someone wanting to build thousands of them and deploy them globally is simple: they’re cheap.
The design of the first of a kind is not cheap compared to a diesel engine that’s been iterated and improved upon thousands of times since its inception. The development of the first commercial product will not be cheap. It will require thousands of attempts at creating, building, testing, destroying, improving, and perfecting a long list of specialized components and working assemblies. But the end product will be cheap – meaning the final solution or end goal in mind should be a product which has orders of magnitude less material, fewer components, and less complexity than a large facility.
Most importantly, the cost of each iteration will be lower than the cost of a large scale plant, which means for the same capital cost you’ll be able to create and test significantly more designs. Yes, upon commercialization you’ll need to sell more designs in order for them to be profitable, and the power and energy demand for them is enormous.
These are all key points critical to innovating, and Paul addressed each as a competitive advantage when discussing his design for the MsNB (Molten Salt Nuclear Battery). To summarize:
- Don’t start from scratch. Leverage what other people have learned and done so far. Paul is leveraging a design developed by the US national lab system in the 1960’s.
- Actually build something to test it. Learn from building it, re-design it, then test it again. While he’s performed computer modeling, he’s also an engineer and realizes a common mantra to be real: all models are wrong – some of them are useful. As such, go out and actually build something to test it empirically.
- In order to innovate, you’ll need to iterate. In order to iterate, you’ll need to make it inexpensively to get lots of tries. Smaller parts and assemblies are cheaper to build than larger parts and assemblies of scaled up geometries. Therefore, start small to go big.
When discussing costs and economic models with Paul, he articulated a tremendously good point. First of a kind machines are always more expensive than the Nth of a kind. The first automobile was tremendously more expensive than modern engines (and much less efficient, reliable, and effective). However, if you continue to build more of them, then they will become cheaper and cheaper and cheaper. It’s inevitable.
The key advantage in utilizing nuclear fuel is the underlying physics are orders of magnitude better at producing heat than lighting things on fire, and therefore it almost doesn’t matter how expensive the first prototype is. It matters how expensive the Nth of a kind is and how long it takes you to get there. But once you’re there, the demand for the power will be so great that any economic model will demand you to sell all your other investments and literally go all in on this one.
Subscribe to our newsletter
Never miss an insight. Subscribe for updates on industry developments, new articles, and podcast releases
Invest with Fire2Fission
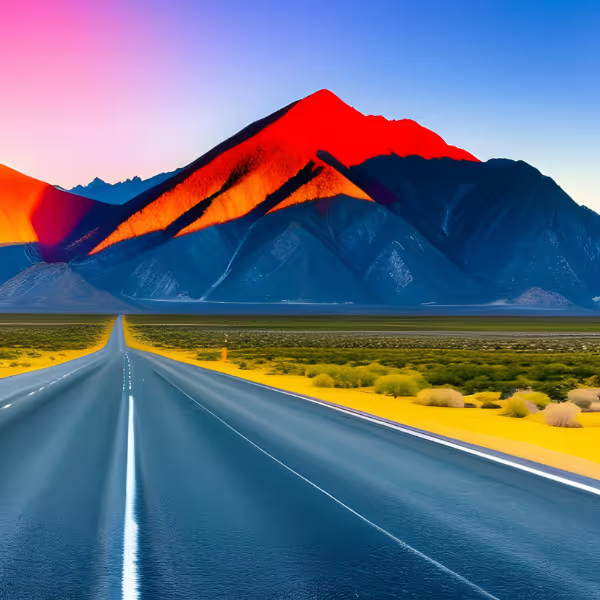